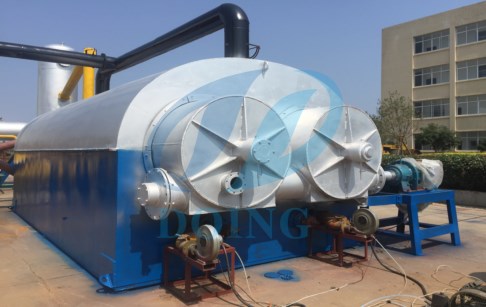
Fully continuous waste tire pyrolysis plant
Doing fully continuous waste tire pyrolysis plant is more popular in the market than batch pyrolysis plant and semi-continuous pyrolysis plant because of the high degree of automation and larger capacity. For the large capacity, the daily capacity can be 30 T. Speaking of the high degree of automation, continuous continuous waste tire pyrolysis plant is equipped with automatic feeding and discharging system, which can realize feeding materials on one side and discharging slag from the other side continuously.
Workflow of fully continuous waste tire pyrolysis plant:

3Ddrawings of fully continuous waste tire pyrolysis plant
1. The processed raw material is put into the pyrolysis reactor automatically. When the inner temperature of the pyrolysis reactor reaches related degree, the oil gas will be generated.
2. Then the oil gas goes into the catalyst chamber firstly. In the catalyst chamber, the heavy oil gas will be liquefied into heavy oil and drop in the heavy oil tank. The light oil gas rise up to the condenser, and then be liquefied into oil. In the hydroseal, the combustible gas will be desulfurated and cleaned then recycled to heat the pyrolysis reactor.
3. The smoke produced when heat the reactor will be cooled down, then enters the de-dusting system. In the spraying tower, the smoke will go through the water washing, water spray, and ceramic ring adsorption, so the smoke can meet the EU environmental protection and emission standards.
4. As for the carbon black, it will be discharged by the auto screw discharger.
Final products of fully continuous waste tire pyrolysis plant:
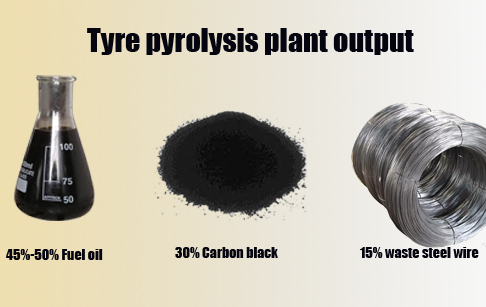
Final products of fully continuous waste tire pyrolysis plant
Both the fuel oil and the carbon black produced by the cracking process can be directly marketed. If you want to get higher market value, you can further process them ,and we have specialized equipment for this,waste oil to diesel distillation machine ,carbon briquetting machine and grinding machine. Fuel oil can be refined to light diesel oil, carbon black can be made into carbon black pellets for combustion, or milling to carbon black fine powder, used in the production of tires, rubber soles, paints and so on. Non-condensable gases can be recovered as fuel heating the reactor, which saves fuel costs.
Advantages of fully continuous waste tire pyrolysis plant:

Fully continuous waste tire pyrolysis plant
1,To adapt rotation outside and to heat reactor by 360°evenly. Without heating any partial reactor for long time, in this way, our reactor has a longer span life.
2, spiral vanes are designed inside the reactor, running the raw materials along the inner wall of the reactor. The raw materials are uniformly advanced in the reactor and directly contacted with the heat transfer surface, immediately receiving heat,so heat exchange is quick and evenly distributed.The process of pyrolysis is greatly improved.
3,The reactor and feeder drive adopt frequency conversion and explosion-proof motor, which can adjust the residence time of the raw material in the reactor according to the pyrolysis of the raw material in the reactor to achieve the purpose of adjusting the treatment amount and the pyrolysis status, so that the raw material can meet the requirements. In the case of the amount of treatment, it is sufficiently decomposed to increase the oil yield.
4,Our reactor can be fed by steel wire-free tire rubber particles and the steel wire-containing tire rubber particles. It can also separate the carbon black from the steel wire when carbon black is discharged, and if The raw materialdoes not include steel wire,then our reactor can increase the processing capacity by 10%, and can be cooled during the process of discharging carbon black and steel wire,and carbon blacks can be directly packaged and collected, the cooling time can be saved, and the production efficiency can be improved.
5, while using the burner as a heat source, our reactor recycles the non-condensable flammable gas generated from the continuous tyre pyrolysis plant and passes the exhaust gas burner as the second heat source of the reactor, achieving “self-sufficiency” and saving The consumption of fuel will reduce production costs and increase revenue for customers. In addition, the flue gas after combustion of the exhaust gas is effectively treated to meet the environmental standards for flue gas emissions.
Contact: Ms Bonnie
Phone: +86-371-5677 1821
Mobile/Wechat/Whatsapp:0086-135-2669-2320
Skype: bonniezhao2
Email: oilmachine@doinggroup.com
http://www.doinggroup.com
http://www.continuouspyrolysisplant.com
VIew more: pyrolysis plant
continuous waste tire pyrolysis plant
Online service>>